Do you need a milk cooling tank?
Call us now
The new milk cooling tank
CHARRIAU sells new open milk cooling tanks from 50 to 2,500 litres, and closed milk cooling tanks from 1,000 to 20,000 litres.

Verticalcylindrical tanks
Verticalcylindrical tanks

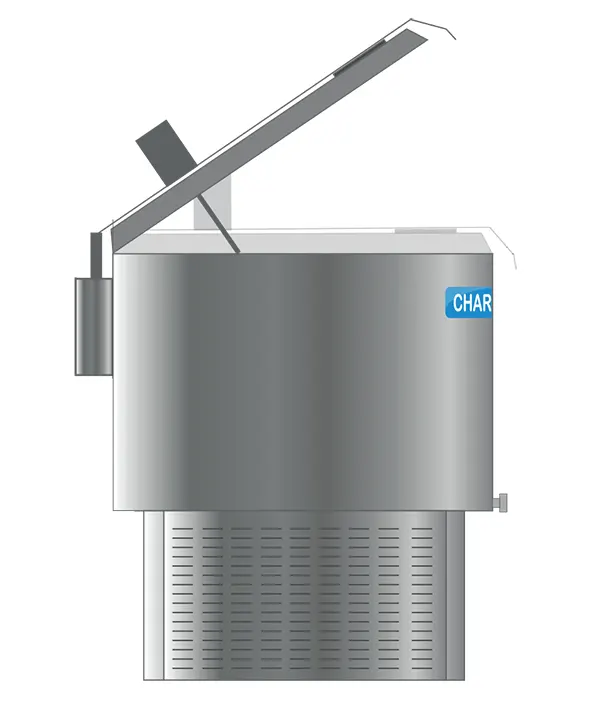
Horizontalcylindrical tanks
Horizontalcylindrical tanks
Please consult us.
General technical specification of the milk cooling tank
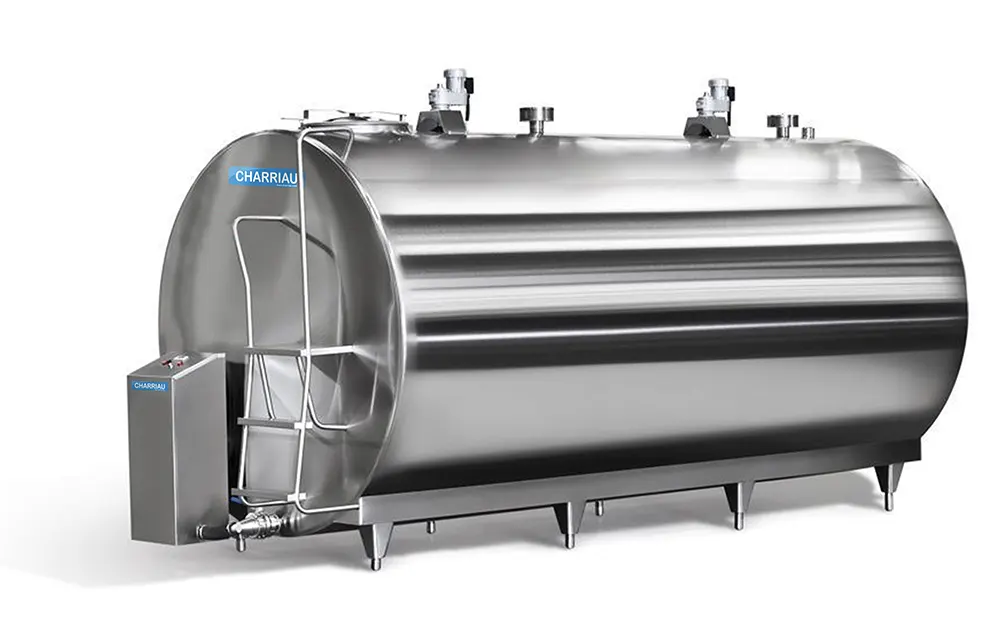
Horizontal cylindrical tank, free positioning, smooth interior surfaces, rounded corners, perfectly polished welds, adjustable feet for uneven floors.
Direct expansion bottom designed to ensure complete emptying of the tank. The design of the evaporator prevents the milk from freezing even with small volumes.
Rupture pressure at 60 bar.
Operating pressure: 30 bar.
Precise insulation by controlled injection of environmentally friendly high density polyurethane foaḿ.
Agitation composed of a three-phase motor reducer Sirem IP55 131 W 25 rpm, a stirring blade in one piece without welding (IC 1000 – IC 2500 L), a three-phase motor reducer Sirem IP55 145 W 21-25 rpm, a one-piece stirring blade without welding (IC 3000 – IC 6000 L), two three-phase geared motors Sirem IP 55 145 W 21-25 rpm, two one-piece blades without welding (IC 8000 – IC 14000 L).
Raised gearmotors for better cleaning.
Milk discharge and evaporator inclination according to international patents (ISO 5708).
Stainless steel measuring ruler and standard measuring table.
Stainless steel butterfly valve DN50 (for IC 1000 – IC 6000), Ø52 mm and stainless steel butterfly valve DN80 (for IC 8000 – IC 14000), Ø85 mm with male thread́, PVC plug with stainless steel chain for all models up to 6000 litres.
Manhole Ø400 mm on IC 1000 to 3000 litres, manhole Ø500 mm on IC 4000 to 14000 litres.
Stainless steel ladder on all models of 2000 litres and more.
Washing tube Ø25 mm with rotating diffuser for perfect washing in every corner of the tank.
No ball diffusers that could be clogged by salts in the water after a period of use.
External stainless steel vent for pressure equalization.
Hermetic type compressor (Tecumseh Hermetic Unit, Danfoss Maneurop, Copeland scroll), R449 refrigerant, solenoid valve, voltage and phase controller (L1-L2-L3) for the protection of the electrical circuits of the tank against voltage variations, high pressure and low pressure switches, high pressure switch for the regulation of the second fan of the cooling circuit, liquid cylinder and liquid sight glass are included for the protection and high performance of the refrigerating unit.
Translated with www.DeepL.com/Translator (free version)
Adopted International Standard: DIN 8968-1986, MOD ; NF U36-101-1987 bulk milk cooler. ; GOST R 50803-1995 refrigerated bulk milk tanks. general requirements ; GOST R 50803-2008, IDT ; DS/ISO 5708-1985,IDT ; NEN-ISO 5708-1984,IDT ; UNE 68-049-82
NF EN 13732-2003 (U36-101) ; NF U36-101-2003 food processing machinery – bulk milk coolers on farms – requirements for construction, performance, suitability for use, safety and hygiene. NF U36-101-2009 food processing machinery – bulk milk coolers on farms – requirements for construction, performance, suitability for use, safety and hygiene.
needfor a milk cooling tank
The dairy must allow for the collection and storage of milk in the milk tank under optimal hygiene and safety conditions
A suitable floor
At least concrete: non-slip and washable.
Slightly sloped to avoid stagnation of water under the tank, with a drain to a collector.
The owner of the milk cooling tank must have the tightness of the refrigeration circuit of his milk cooling tank checked by an approved body when it is put into service and then annually.
To ensure proper operation of the milk cooling tank, its installation should be integrated into the design of the building.
Consultation with the dairy’s refrigeration department or the milk cooling tank supplier is essential before finalising the project in order to properly size the milk cooling tank and position the electrical, drinking water and milk inlets, drains and ventilation.
Translated with www.DeepL.com/Translator (free version)
Daily maintenance
Washing
After collection, once washing is complete, check
by eye and nose the cleanliness of the tank, which should be free of any deposits. Also keep the outside of the milk tank clean, especially the milk tank outlet valve (inside and outside). Check any warning lights on the milk tank console.
.
In case of problems
To be checked
- Washing parameters (including water temperature and concentration of products used)
- That the water inlet filters are not clogged.
Measuring the smooth operation of the agitator
Necessary to homogenise the milk from the various milkings and ensure uniform cooling, the agitator normally rotates continuously during the cooling time and then during storage for 2 minutes every 13 minutes. You can check the operation by standing near the milk tank for a quarter of an hour and checking that these time intervals are observed. A problem with the agitation can be suspected in particular in the event of a sudden and unexplained variation in the fat content of the milk.
Translated with www.DeepL.com/Translator (free version)
Never change the stirring speed
Cooling
Check the temperature of the milk in the tank daily :
Immediately after milking, the milk must be cooled to between 0 and 6°C within a maximum of 3 hours, regardless of the volume to be cooled, except in the case of food business operators meeting the requirements of Regulation (EC) No 853/2004.
The temperature is usually displayed on the milk cooling tank. If in doubt about the operation of the thermostat, do not hesitate to check it manually with a thermometer.
Check the operation of the warning lights on the milk tank console.
Keep the condenser clean and clear.
As the lungs of the cooling system, it must be kept clear and cleaned regularly to ensure good heat exchange with the outside.
A dirty condenser increases the cooling time of the milk and increases the electricity bill.
Dusting can be done with a dry nylon brush. (Do not use metal brushes, which may damage the fins, and do not use a high-pressure cleaner, which may crush them).
Pay particular attention to the cleanliness of condensers during hot weather.
Take out the dipstick after washing
The gauge must be clean, dry and on the outside of the milk tank on the counter provided.
Keep the gauging chart in a visible, well positioned and well maintained place.
IN THE EVENT OF A THUNDERSTORM
- If you unplug your milk tank, do not forget to turn it back on after the storm.
- Check with your dairy to find out what to do in the event of a storm.
- Never work on the electrical circuit alone (call in the chosen service provider or the dairy)
To control the electricity consumption of the milk cooling tank
There are other ways to control the electricity consumption of the milk cooling tank:
- Install part of the milk cooling tank (the rear part with the cooling unit) outside under a well-ventilated closed shelter.
- Install the cooling unit outside (milk cooling tank with separate cooling unit)
- Install a milk pre-cooler, which reduces by about 50% the power consumption of the milk tank.
Source : INSTITUTE OF ANIMAL HUSBANDRY – STORAGE AND CONSERVATION OF MILK ON THE FARM